When it comes to ensuring the safety of the products we consume, cartridge filtration systems are at the forefront of the manufacturing process throughout all sectors in the beverage production industry. The advancement of filtration technology, and increasingly stringent food and hygiene regulations have truly transformed food and beverage manufacturing over recent decades, both enabling and forcing producers to tightly control the quality, taste, appearance and longevity of beverage products.
Beverage industry sectors and cartridge filter applications
Filtration plays a critical role in the process of beverage products, from brewing an iconic beer to distilling a world-famous gin – none of which is possible without the right filter systems in place. Let’s take a closer look at which solutions are used and why, below.
Brewing filtration
Beer brewing companies heavily rely on durable and reliable cartridge filtration systems to achieve the consistent brewing results, from bottle to bottle and brewery to brewery.
Top contaminants such as spoilage organisms that can enter the beer making process can damage that all-important taste, while solids and yeast can ruin the brew’s distinctive clarity, all of which can have disastrous knock-on effects, costing the manufacturer significant time and money.
Cost is key when it comes to selecting the right type of filtration system, as many brewers find that the range of filterability levels required can dramatically alter the cost of filtration.
Types of filters used: polypropylene depth filters, sterile gas filters, pleated depth filters, PES membrane filters.
Filters are used for: visual clarity, improving/maintaining desired taste and odour by removing contaminants and spoilage organisms, incoming water and gas filtration and to ensure shelf life.
Soft drinks filtration
Loved by millions, if not billions of people around the world, soft drinks continue to be a number 1 favourite beverage for humankind. The typical ingredients that make most
Soft drinks are carbonated water, sugar, and flavoured additives, with water being particularly key to not only the active ingredients list but also to the manufacturing process itself, as it is used in cleaning, washing and boiler feed applications too.
Top water sources available to sift drinks manufacturers are mains, borehole, rivers, and springs. In mains supply the key concerns are the removal of chlorine, particulate, and spoilage organisms. With borehole sources then turbidity reduction, removal of particulates and spoilage organisms are the main concerns.
Types of filters used: Bag filters, sterile gas PTFE membrane, pleated depth filters and depth filters.
Filters used for: water supply filtration, removing CO2, syrup filtration.
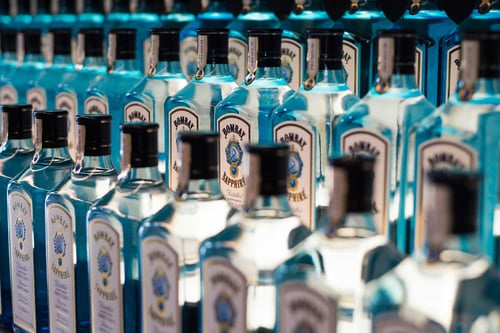
Sprits filtration
In the world of spirit production, colour, stability, and clarity are vital in producing a successful final product. To achieve the desired taste and aesthetics, plus maintain product integrity, filtration is critical to the spirit manufacturing process.
The two main challenges that light spirits manufacturers usually face in the distilling to bottling process are the removal of particulates and the prevention or removal of chill hazes, which occur in the cooling process and result in a cloudiness or haze, visible to the naked eye. Careful consideration and selection of appropriate filter products is required when removing hazes, to ensure that esters are not removed, which would impact the desired characteristics of spirit.
A common filtration process used in darker spirits (whiskey, rums) manufacturing, is the removal of what is known as ‘char’. Charred barrels are used because the char absorbs and removes certain compounds and enhances the whiskey flavour; however, issues arise when small particles of charred wood are released into the whiskey during maturation. These particles therefore need to be removed via cartridge filters prior to bottling.
Types of filters used: Depth filters, pleated depth filters, carbon filters and hygienic strainers.
Filters used for: de-colorization/removal of natural pigments to control aesthetic, contaminant removal to improve and control taste and odour, particulate removal, char removal and preventing and removing chilled hazes.
Your Filtration Systems Partner
If you are searching for a new filter solutions’ partner for your industrial filter application, whether its Food & Beverage, Chemicals & Solvents, Medical or Process Water, PoreFiltration are the ideal supplier to support you. We source the most cost effective, reputable, and readily available filter system products on the market, giving you the competitive edge against your rivals. Get in touch for a quote today.