Sterile Gas and Vent Filters
New or replacement sterile gas filters for all applications
Sterile air and gas filtration is essential for preventing microbial contamination in food and beverage processing, pharmaceutical manufacturing, and other critical applications. These filters remove microorganisms from air and process gases, ensuring that ingredients, products, and equipment remain protected from airborne contaminants. They also protect tanks & product storage vessels, as they breathe during filling & emptying, from local environment contamination.
In addition to these sterile-grade filters, gas PTFE membrane and GF pleated depth, we provide high-performance coalescing filters, for prefiltration to ensure removal of liquid aerosols and fine particulates from compressed gases. These coalescing filters enhance the performance and longevity of the final sterile filter by reducing the contaminant load, ensuring maximum protection in sterile gas applications.
All filters in our range are designed for low differential pressure operation, helping to minimize energy consumption and extending service life; ultimately lowering overall running costs while maintaining the highest levels of sterility assurance and reglatory compliance.
Sterile Gas PTFE Membrane Filters
Our PTFE membrane filter range includes filters for retrofiting and HighFlow filters for new sterile gas or vent applications. All filters are validated at 0.02 micron.
Sterile Gas Depth Filters
Our depth filter range includes HighFlow pleated GF filters for new sterile gas or vent applications wrapped GF depth filters for retrofit. All filters are validated at 0.02 micron.
Frequently Asked Questions
Sterile gas filtration removes particles, bacteria, and other contaminants from a gas stream to ensure it is free from harmful microorganisms. This process is essential in industries where gas purity is critical to product safety and quality.
Sterile gas filtration prevents contamination in sensitive processes, ensuring regulatory compliance and product integrity. Industries such as pharmaceuticals, biotechnology, food & beverage, and semiconductor manufacturing rely on sterile gas filtration to protect products from microbial contamination and particulate ingress.
There are two primary types of sterile gas filters:
- Sterile Gas Membrane Filters: Made from PTFE, PVDF, or PES, membrane filters offer absolute retention and high bacterial removal efficiency.
- Sterile Gas Depth Filters: Pleated glass microfiber or wrapped depth media for high flow capacity plus particle and microbial retention. These filters are particularly useful in autoclave or lyophilisation applications where vacuum has to be broken very quickly.
For applications like cleanrooms, medical facilities, and operating booths that require large volumes of high-purity, low-pressure air, HEPA filters are the optimal choice. They efficiently remove sub-micron particles, ensuring the cleanliness essential in these environments.
Sterile gas filtration is widely used in:
- Pharmaceutical Manufacturing: Sterile air supply for lyophilization, fermentation, and bioreactors. Also Sterile Venting of product and transfer tanks is used extensively.
- Food & Beverage Processing: Sterile filtration of compressed air used in aseptic packaging and fermentation. In application where CO2 is use for carbonation of liquids the CO2 is filtered to ensure there are no contaminates transferred to the gas.
- Medical Device Production and Semiconductor Manufacturing: Contaminant-free air for sterile medical device packaging and cleanrooms plus the protection sensitive processes from airborne particles and contaminants in semiconductor manufacturing.
Filters are tested using different methods depending on the filter type:
Sterile Gas Membrane Filters (PTFE, PVDF):
-
Bubble Point Testing: Ensures membrane integrity by measuring the pressure at which air bubbles pass through a wetted filter.
-
Diffusion Testing: Measures gas flow through the membrane to check for defects.
-
Pressure-Hold Testing: Verifies filter performance by ensuring consistent pressure retention.
The difficulty with testing hydrophobic filters, which PTFE and PVDF both are, is wetting out the filters to perform these tests. Typically 60:40 IPA/Water is used, but this is a time consuming process and filters are normally tested off-line rather than in-line as is the case with most sterile liquid membrane filters.
Sterile Gas Depth Filters:
Depth filters are not absolute-rated and do not have a defined pore size like membranes, so standard integrity tests (e.g., bubble point) are not suitable. Instead, their integrity is assessed aerosol challenge testing:
This method involves challenging the filter with a standardised aerosol containing particles of known sizes. It assesses the filter’s retention efficiency under realistic operating conditions. Aerosol challenge testing is particularly useful for verifying the performance of high flow sterile gas depth filters and wrapped depth filters, ensuring they maintain microbial removal efficiency even under high load conditions. This is also the common method used for testing HEPA filter.
Consider the following factors:
- Gas Type & Flow Rate: Ensure the filter can handle the required volume and pressure.
- Pore Size & Filter Media: Membrane filters for sterility, depth filters for high particulate loads.
- Regulatory Requirements: Compliance with ISO, FDA, USP, or GMP guidelines.
- Filter Configuration: Pleated GF for high-capacity applications, wrapped GF for standard sterile filtration in F&B and non-critical applications, and membrane filters for critical sterility.
Read more in our blog: Ensuring You Use The Optimum Sterile Gas Filter
Key factors include:
- Contaminant Load: Higher particle loads reduce filter lifespan.
- Operating Conditions: Pressure, temperature, and humidity can affect filter integrity.
- Regular Maintenance & Testing: Routine checks extend filter life and ensure efficiency.
- Filter Medium: Pleated Sterile Gas Depth filters have a longer life in high-dirt environments compared to PTFE membrane filters, which may clog faster in the presence of heavy particulates.
- Correct Selection of Prefiltration: Coalescing depth filters provide the highest level of protection and help extend final sterile gas filter service life regardless of whether they are either pleated or wrapped GF or PTFE membrane filters.
Read out blog: Why Prefiltration is Key in Continuous Filtration Processes.
Sterile gas filters should comply with:
-
ISO 13408-2: Validation of aseptic processes.
-
USP <797> & USP <800>: Standards for pharmaceutical compounding and sterile processing.
-
FDA & GMP Requirements: For pharmaceutical and food applications.
Choosing a filter that meets these standards ensures compliance with industry regulations.
-
Regular Integrity Testing: Ensure the filter is still performing as expected.
-
Scheduled Replacements: Change filters based on differential pressure drop. Your manufacturer should provide changeout guidelines, which is typically at 2.5 bar differential pressure.
-
Cleaning & Sterilisation: All sterile gas filters, can be steam-sterilised prior to use and the number of steam cycles acceptable will determine service life.
-
Pre-filtration: Normally coalescing depth filtration offers the best final sterile gas filter protection and helps maximise the lifespan of sterile gas filters.
Read more here: 6 Tips to Achieve Continuous Effective Gas Sterilisation.
-
Increased Differential Pressure Drop: Indicates clogging; consider pre-filtration with a depth filter.
-
Sterility Test Failures: Check integrity test results or ensure correct installation.
-
Filter Lifespan Issues: Review gas quality, consider pre-filtration, or switch to a longer-life filter like Sterile Gas Depth Filter.
Initial correct system design and ongoing maintenance reduce downtime and yearly filtration costs.
Explore Related Articles
All our filter products are manufactured to the highest quality standards with certificates of conformity and validation guides that can be provided upon request.
- All filters used in the food & beverage markets are EU and FDA compliant for material in food contact. Additionally certain products are Halal or Kosher certified.
- Filters for use in healthcare or pharmaceutical applications meet the requirements of US FDA 21 and evaluated in accordance with USP Class VI plastics.
- Products provided for automotive use in paint systems are silicone free.
Talk to us today about your filtration requirements
-
Extensive product range
-
Best Price GUARANTEED!
-
Specialist support team with deep knowledge of liquid & gas applications
-
Reliable quality & delivery
Customers We Work With
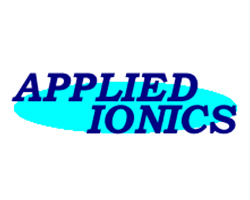
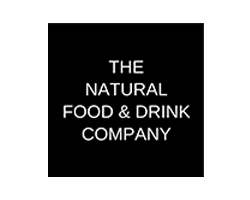
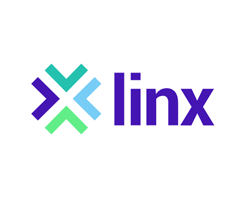
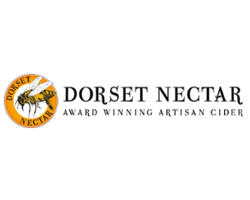

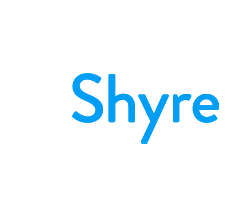
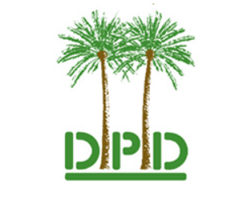
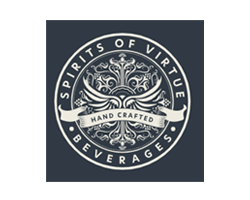