Glossary of Filtration Terms
Demystifying some of the technical terms used in filtration.
Absolute Filtration
A process that removes particles above a specific size, ensuring a 100% removal efficiency for those particular particles from the fluid.
Absolute Rating
The diameter of the largest hard spherical particle that will pass through a filter under specified test conditions. It is an indication of the largest opening in the filter pore size in a filter medium.
Backwashing
The process of reversing the flow of liquid through the membrane to dislodge and remove accumulated particles or fouling materials.
Bag Filter
A bag filter is a material bag (Polypropylene, Polyester, PTFE, Nylon mesh) that traps solid particles suspended in either a gas or a liquid.
Beta Ratio
The ratio of the number of particles upstream of the filter to the number downstream, indicating filtration efficiency and is defined as:
β = Number of particles of a given size and larger in the influent / Number of particles of a given size and larger in the effluent
A β = 5,000 can be used as an operational definition of an absolute rating.
Bubble Point
The pressure at which gas bubbles penetrate and pass through a wetted membrane, indicating pore size and integrity.
Bubble Point Test
The most widely used non-destructive integrity test is the bubble point test. Bubble point is based on the fact that liquid is held in the pores of the filter by surface tension and capillary forces. The minimum pressure required to force liquid out of the pores is a measure of the pore diameter.
Bypass Valve
A safety feature allowing fluid to bypass the filter when the pressure drop exceeds the set limit.
Carbon Filter
A carbon filter uses activated carbon to remove impurities from water or air through adsorption, where contaminants adhere to the carbon's surface. It effectively removes chlorine, pesticides, volatile organic compounds (VOCs), and odors.
Cartridge Filters
A size format used in industrial and manufacturing scale applications. Other formats include capsules & disposables for laboratory use, and junior sizes for development use.
Changeout Differential Pressure
The ΔP at which fluid flow is too low to continue using the cartridge or bag filters. Typically, this is 36 psi (2.5 bar) for cartridges and 15 psi (1.0 bar) for bag filters.
Clean Differential Pressure (ΔP)
Also known as the initial or design differential pressure but is the value when a filter is newly installed in a system. Typically, this is 2 psi (0.140 bar) for a liquid system.
Clean Pressure Drop
The initial pressure drop across the filter when it is clean and new.
Clogging
Accumulation of particles that obstruct the filter media, reducing efficiency.
Cold Pastuerisation
Cold pasteurisation in the beer industry is a method of beer sterilization that uses microporous membrane filters instead of heat to eliminate microorganisms. It's used to preserve the quality of heat-sensitive beers, like draught beer.
Collapse Strength
The ability of the filter cartridge to resist deformation or collapse under pressure. Typically this is set at differential pressure of 5 bar for cartrigde filters.
Colloid
A suspension of submicron particles in a fluid that won't settle out
Contaminant
An undesirable solid or gelatinous particle in a fluid
Cross-Flow Filtration or Tangential Flow
A filtration technique where the liquid flows parallel to the membrane surface, promoting continuous cleaning and reducing fouling by maintaining shear forces on the membrane surface.
Dead-End Filtration
A filtration method where the liquid flows perpendicular to the membrane surface, and particles are retained on the membrane, leading to potential clogging and lower efficiency compared to cross-flow filtration.
Depth Filters
Liquids pass through a tortuous maze of filter fibres that gradually become more compact. As the fluid passes further through this filter bed, smaller and smaller sizes of particulate contamination are removed by a filtration mechanism known as direct interception (or mechanical sieving). Commonly these are manufactured in polypropylene or glass fibre.
Depth Filtration
Filtration that occurs throughout the depth of the filter medium.
Differential Pressure
Differential pressure is essentially the difference in pressure between two given points. For a filter it is measured between the inlet and outlet of the filter housing that the filter is housed in.
Dirty Pressure Drop
The pressure drop across the filter when it is loaded with particles and needs replacement or cleaning.
End Caps
The top and bottom components of the filter cartridge that hold the filtration media in place.
Filter Housing
The casing or vessel that holds the filter cartridge.
Filtrate
The clear liquid that remains after filtration.
Filtration
The process of separating particles from a liquid or gas using a filter.
Filtration Efficiency
The ability of the filter to remove particles of a specified size.
Flow Rate
The volume of fluid passing through the filter per unit of time.
Flux
The rate of flow of a liquid through a membrane surface during microfiltration, often measured in litres per square meter per hour (LMH) or gallons per square foot per day (GFD).
Fouling
The accumulation of particles, microorganisms, or substances on the surface or within the pores of the membrane, reducing its effectiveness and efficiency.
Gasket
A seal used to prevent leaks between the filter cartridge and the housing.
Maximum Differential Pressure
The maximum pressure difference allowed across the filter.
Maximum Operating Pressure
The highest pressure a filter can withstand without damage.
Mechanisms of Filtration
Suspended solids are separated from fluids via three mechanisms: direct interception, inertial impaction, diffusional motion and.
- Direct interception - This type of mechanism is characterized by a particle that follows a fluid streamline and does not deviate from that streamline.
- Inertial impaction - Inertial impaction refers to a particle's inability to follow sudden change in fluid flow direction.
- Diffusional motion - The random motion by small particles suspended in the fluid. It is a zig-zag motion of the particles. The particles move randomly as they are bombarded by molecules in the fluid causing them to become larger from a filtration perspective and easier to remove.
Membrane
A semi-permeable material used in microfiltration that allows certain substances to pass through while blocking others based on size and characteristics.
Membrane Filters
A microporous synthetic semi permeable structure manufactured from PES, Nylon, PTFE, and Cellulose that is used to reduce or completely remove microorganisms or bacteria from a fluid. Typically, these are 100 microns thick.
Membrane Integrity Testing
Methods used to assess the effectiveness and integrity of the membrane, ensuring proper filtration. Testing include bubble point, pressure decay and forward flow tests.
Microfiltration
Microfiltration is a filtration process using a microporous medias, membrane and depth filters, that retains the suspended solids of a fluid. Sometimes also called Process Filtration this dead-end filtration technology works in a range between 0.1 micron to 40 microns.
Micron
1 micron is 0.001mm (1/1000 of a millimetre). A pencil point is about 40 microns or 0.040mm (40/1000 of a millimetre) and one of the smallest things an unaided eye can see.
Nominal Rating
An arbitrary micron value assigned by the filter manufacturer, based upon removal of some percentage of all particles of a given size or larger. It is rarely well defined and typically not reproducible.
Non-Destructive Testing
Non-destructive testing may be done on filters before and after use. Integrity testing sterilizing filters before use monitors filter integrity prior to batch processing, preventing use of a non-integral filter. Forward flow, pressure decay or bubble point are common non-destructive intergrity tests
Oil Removal Filters
Oil adsorbing filters are made either of activated carbon or, more recently, modified cellulose media, which is extremely effective in reducing levels of hydrocarbons in a water supply, leaving it markedly cleaner, and better-suited for a number of applications.
Particle Loading Capacity
The amount of particles a filter can hold before requiring replacement or cleaning.
Permeate
The filtered liquid that passes through the membrane, leaving behind impurities and particles in the retentate.
Pleated Cartridge
A filter cartridge with pleats, increasing the surface area and dirt-holding capacity.
Pore Size
The diameter of the microscopic pores in a membrane, determining the size of particles or microorganisms that can pass through.
Porosity
The percentage of void space in a filter media or cartridge, also known as voids volume.
Post-Filtration
Subsequent filtration to remove smaller particles that pass through the initial filter.
Prefiltration
The purpose of a prefilter is to reduce overall operating cost by extending the life of the final filter. Typically, depth filters are prefilters to membrane filters.
Pressure Drop
The decrease in pressure as fluid flows through the filter due to resistance from the filter media.
Pressure Hold Test
The Pressure Hold Test, also known as pressure decay or pressure drop test, is a variation of the diffusion test. In this test, a highly accurate gauge is used to monitor upstream pressure changes due to gas diffusion through the filter. Because there is no need to measure gas flow downstream of the filter, any risk to downstream sterility is eliminated.
Retentate
The concentrated solution or suspension containing particles, microorganisms, or substances that are retained by the membrane during filtration.
Retention Efficiency
The percentage of particles retained by the filter media of a particular micron size.
Service Life
The duration a filter can effectively function before replacement.
Silt Density Index (SDI)
Silt Density Index is a measure of the amount of suspended solids and colloidal material in water. It's used to determine how the water will the efficiency and performance of reverse osmosis (RO) membranes. Any value over 5 will require the use of cartridge filters to improve the water quality before entering the RO.
Sterile Gas or Air Filtration
Final or sterile air filtration removes microorganisms from air or other gases, to protect contacted food and beverage products, ingredients, packaging and equipment surfaces from airborne microbial contamination.
Surface Area
The total area available for filtration within the cartridge.
Surface Filtration
Filtration occurring primarily on the surface of the filter medium.
Sterile Vent Filter
Vent filters are self-contained, compact filters designed to provide high efficiency removal of airborne bacteria and particulate under dry and moist conditions to protect product, storage and balancing tanks as they breath during filling and emptying.
Turbidity
Turbidity is a measure of how clear water is, or how much matter is suspended in it. Turbidity can be caused by natural processes like erosion and precipitation, or by human activities like wastewater discharge.
Zeta Potential
The electrical potential at the shear plane of a particle or membrane surface, influencing particle behaviour and membrane fouling.
Customers We Work With
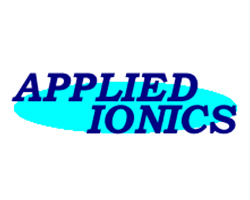
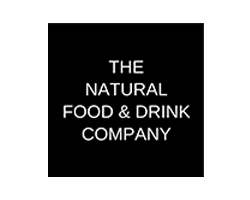
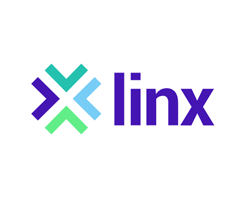
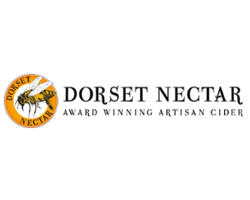

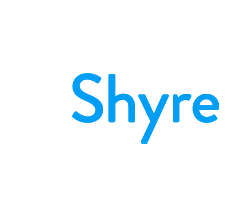
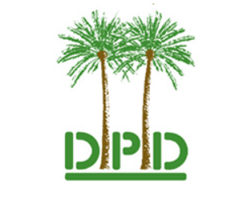
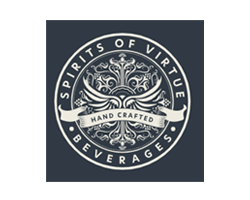
Talk to us today about your filtration requirements
-
Wide range of cartridge and bag filters to retrofit any existing installation.
-
Best Price GUARANTEED!
-
Our experts will optimise your filter systems to further reduce costs.
-
A talented and highly specialist team to support all your filtration needs.
-
Reliability in quality, delivery and support.